Learn How to Increase Your Machining Productivity
When thinking about the evolution of conventional machining processes, previously supported only by mechanical lathes, milling machines or drills, we now have CNC lathes, turning centers and modern machining centers. These tools allow the complete machining of parts and even in a single fixation, such as can be performed on the ROMI DCM 620-5X Vertical Machining Center.
Whatever the size of your business, boosting productivity in machining is key to maintaining your competitiveness. In addition to the technological transformation provided by the modernizing of the industrial park, it is possible to obtain significant results by adopting good practices, while also focusing on people and processes. Here are some tips that will help you design more productive machining processes for your business:
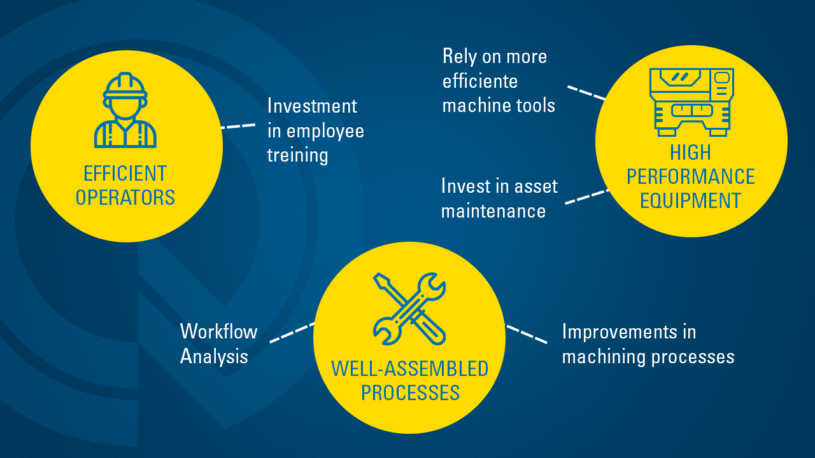
1. Review Existing Workflow
A good way to increase machining productivity is to identify workflow points that need attention. For this, it is necessary to visually map all the steps necessary for the manufacture of your products, understanding the inputs and outputs of each process, the procedures, resources needed, responsibilities, execution time and metrics.
Consider creating detailed flows for monitoring each process. Thus, it will be easier to identify areas with potential improvements, failures, delays, bottlenecks, or capacity problems, and make it possible to implement solutions and improvements.
2. Invest in Employee Training
The manufacturing industry including machine tools and cutting tools is constantly evolving. We are creating and implementing new technologies that make equipment more robust and more productive. Given this scenario, it is common for employees to require development and improvement of different skills needed to perform certain tasks.
Therefore, it is important to have an ongoing training program to ensure that your employees are taking full advantage of the capabilities of the machine tools and their peripherals. When properly trained, employees are more motivated and work more optimally, always seeking to deliver better results.
3. Study Improvements to Machining Processes
To meet the expectations and requirements of a customer of machined items, the development of an adequate, productive, and economical manufacturing process is indispensable. Each item to be manufactured has particularities that make its production process unique, either due to its constructive complexity, material, or finish.
Detailed machining studies, considering all aspects of the part to be developed – and here we talk about items such as parameters, tools and cutting conditions – allow us to analyze the process variables and seek appropriate solutions to obtain the best results. We also emphasize that in a machining process, just like any other process, we must seek continuous improvement, while introducing new technologies or possibilities.
4. Count on Smarter Machine Tools
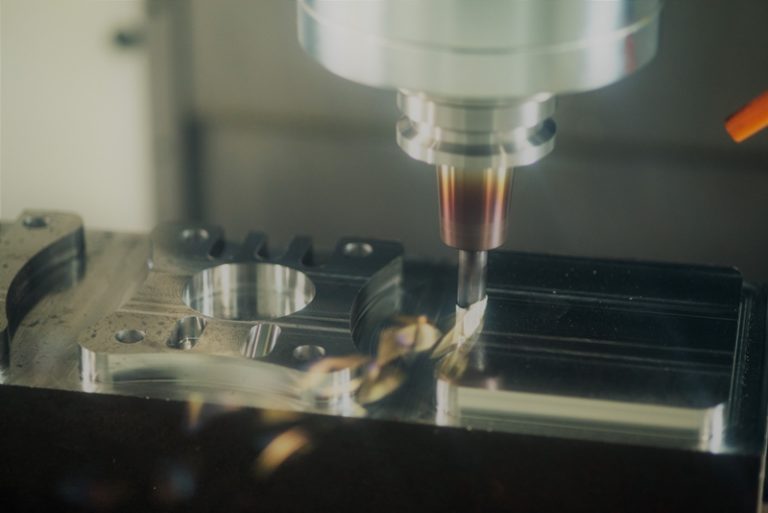
The evolution of machine tools, specifically in the area of computerization, digital controls, equipment and product development systems, and production controls, greatly impacts our ability to make machining more efficient and flexible. These “smart” features act as true operations centers.
Relying on CNC lathes, machining centers, turning centers and other tools with a high level of robustness and precision, is essential to guarantee more machining productivity. Given this scenario, today it is possible to produce much more, even in the face of complex production needs, while reducing costs and increasing the precision and quality of production.
The integration capability of machine tools is also contributing to the creation of much smarter and automated machining processes. An example is the Romi D Series Vertical Machining Center. All Romi D Series have a thermal compensation system, designed to reduce the effects of temperature oscillation on the dimensional aspects of machined parts.
By collecting the temperature data from sensors positioned in strategic locations, the CNC corrects the actual position of each axis, making the position of the tool follow accurate precision and enabling stable dimensional results even over long periods of work.
5. Invest in Asset Maintenance
Good maintenance management has a considerable impact on the costs associated with machine downtime, as well as on the time and budget invested in corrections. For this, it is essential to conduct routine maintenance of assets, which is appropriate for the company’s production schedule. The schedule should include routine inspections, and scheduling of preventive maintenance. New equipment can boost productivity, but it is also necessary to ensure its longevity and its correct functioning.